Anodizing vs. Hard Anodizing: The Differences in Surface Treatment Techniques
Anodizing and hard anodizing are both electrochemical surface treatment processes used to enhance the properties of aluminum and its alloys. While they share similarities, they differ significantly in process parameters, outcomes, and applications. Here's a detailed comparison:
First. Process Overview
Anodizing (Standard Decorative Anodizing):
Forms a thin, corrosion-resistant oxide layer on aluminum.
Second. Hard Anodizing (Type III Anodizing):
Creates a much thicker, denser, and harder oxide layer .
Uses a sulfuric acid (or mixed acid) electrolyte at near-freezing temperatures .
Higher voltage and current density are applied, resulting in a wear-resistant finish.
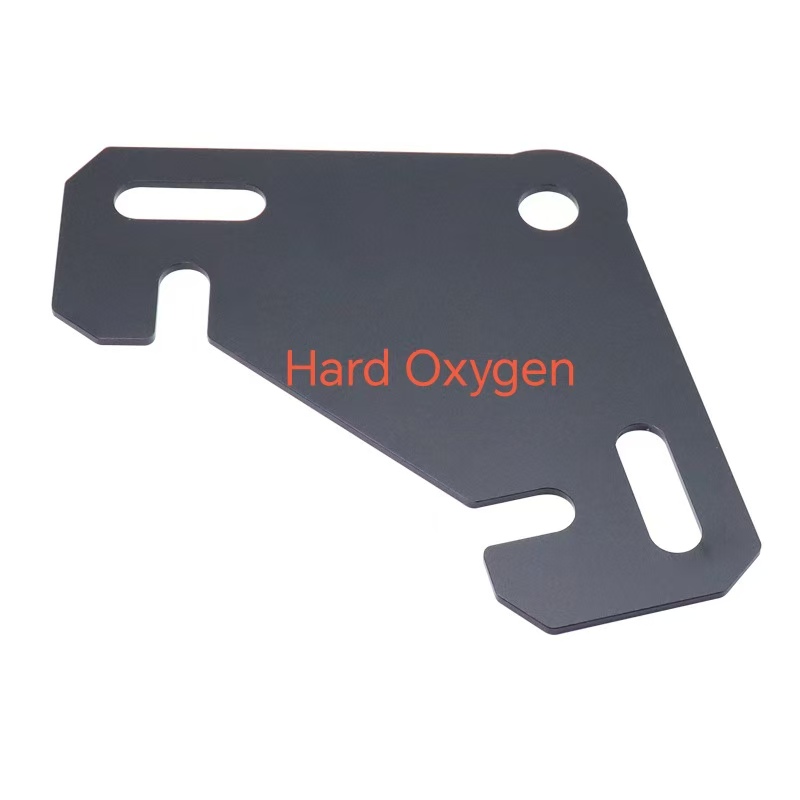
Third. Applications
Standard Anodizing:
Decorative finishes (consumer electronics, automotive trim).
Moderate corrosion protection (architectural components, household items).
Hard Anodizing:
High-wear applications (military, aerospace, firearms).
Industrial components (hydraulic pistons, gears, valves).
Medical and marine equipment (where extreme durability is needed).
Fourth. Post-Treatment
Both processes may involve sealing (hot water or chemical sealing) to close pores and improve corrosion resistance.
Hard anodized parts often undergo PTFE (Teflon) impregnation for reduced friction.
Conclusion
Choose standard anodizing for aesthetics and moderate protection.
Opt for hard anodizing when extreme durability, wear resistance, and corrosion protection are critical.
Would you like details on specific alloys or processing techniques?
First. Process Overview
Anodizing (Standard Decorative Anodizing):
Forms a thin, corrosion-resistant oxide layer on aluminum.
Uses a sulfuric acid electrolyte at room temperature .
Produces a porous surface that can be dyed in various colors.
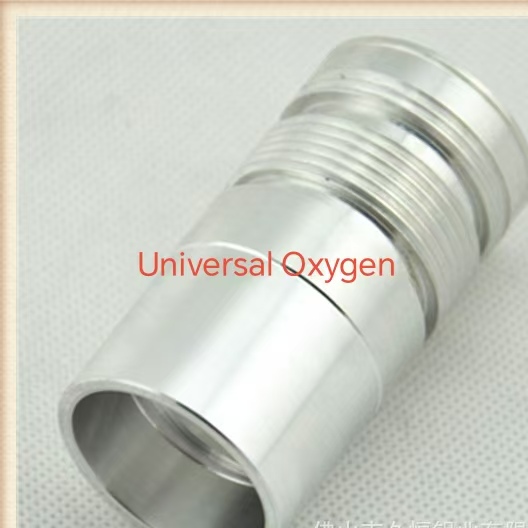
Creates a much thicker, denser, and harder oxide layer .
Uses a sulfuric acid (or mixed acid) electrolyte at near-freezing temperatures .
Higher voltage and current density are applied, resulting in a wear-resistant finish.
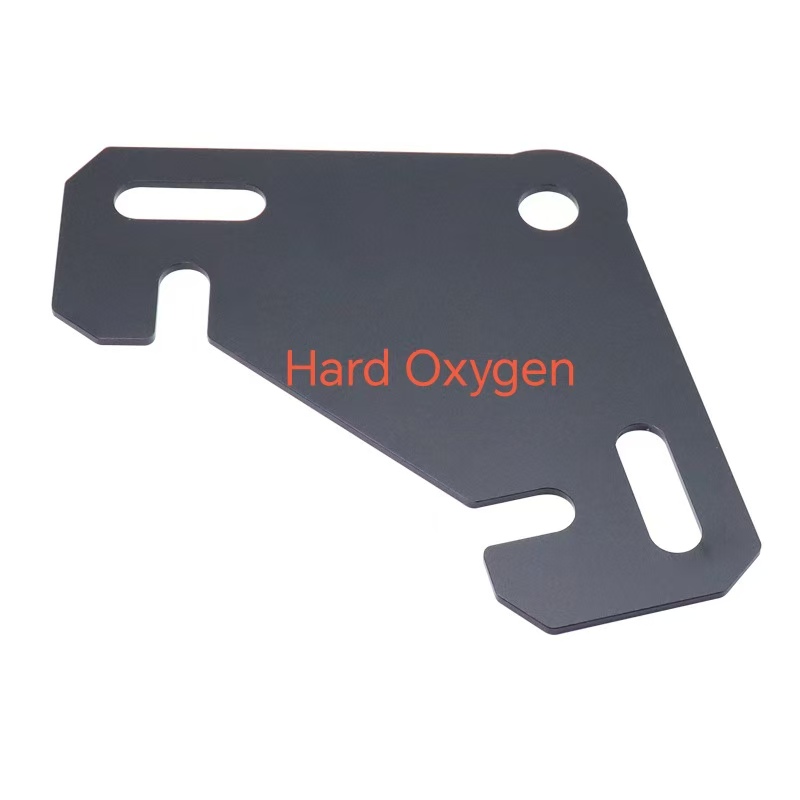
Third. Applications
Standard Anodizing:
Decorative finishes (consumer electronics, automotive trim).
Moderate corrosion protection (architectural components, household items).
Hard Anodizing:
High-wear applications (military, aerospace, firearms).
Industrial components (hydraulic pistons, gears, valves).
Medical and marine equipment (where extreme durability is needed).
Fourth. Post-Treatment
Both processes may involve sealing (hot water or chemical sealing) to close pores and improve corrosion resistance.
Hard anodized parts often undergo PTFE (Teflon) impregnation for reduced friction.
Conclusion
Choose standard anodizing for aesthetics and moderate protection.
Opt for hard anodizing when extreme durability, wear resistance, and corrosion protection are critical.
Would you like details on specific alloys or processing techniques?