Why Is It Important to Polish Titanium Parts?
Polishing titanium parts is crucial for several reasons, each contributing to the material's performance and suitability across various applications:
First. Enhanced Corrosion Resistance:
Polishing creates a smoother surface with fewer micro-imperfections, reducing areas where corrosive agents can accumulate. This promotes a more uniform and effective natural oxide layer (TiO₂), crucial in harsh environments like marine or chemical processing.
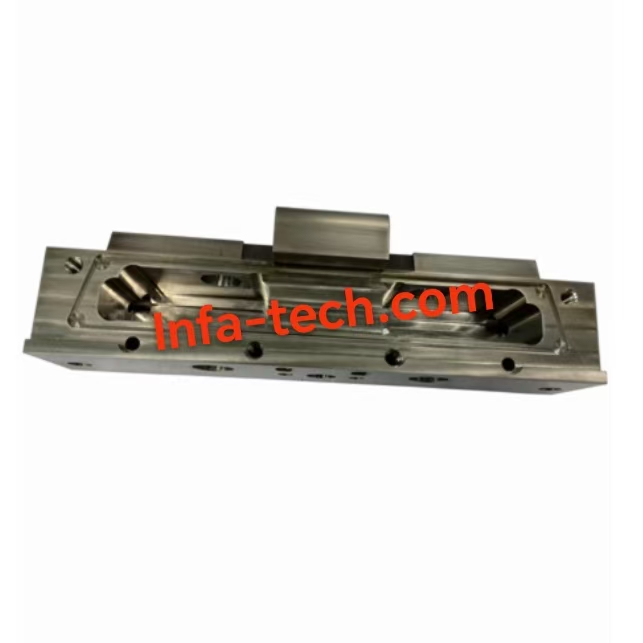
Second. Improved Fatigue Resistance:
Surface irregularities act as stress concentrators, initiating cracks under cyclic loads. Polishing removes these imperfections, extending the component's fatigue life, vital in aerospace and automotive industries.
Third. Reduced Friction and Wear:
A polished surface minimizes friction in moving parts, such as engine components or medical devices, reducing wear and enhancing longevity.
Fourth. Biocompatibility and Hygiene:
In medical implants (e.g., joint replacements), a smooth surface prevents bacterial adhesion, reduces tissue irritation, and ensures easier sterilization, critical for patient safety.
Fifth. Aesthetic Appeal:
Polishing provides a sleek, reflective finish desirable in consumer products (e.g., jewelry, watches) and architectural elements, enhancing visual and market value
Sixth. Precision in Assembly:
Smooth surfaces ensure tighter tolerances and better sealing in high-precision applications, such as aerospace fittings or semiconductor equipment, preventing leaks or misalignments.
Seventh. Prevention of Material Adhesion:
In chemical or food processing, polished surfaces resist deposit buildup, simplifying maintenance and reducing contamination risks.
Industry Examples:
- Aerospace: Polished components withstand fatigue and corrosion in critical structures.
- Medical: Implants benefit from biocompatibility and hygiene.
- Automotive: Reduced friction improves engine efficiency.
- Consumer Goods: Aesthetic polish boosts product appeal.
In summary, polishing titanium optimizes its inherent properties, ensuring reliability, durability, and functionality across diverse applications.
First. Enhanced Corrosion Resistance:
Polishing creates a smoother surface with fewer micro-imperfections, reducing areas where corrosive agents can accumulate. This promotes a more uniform and effective natural oxide layer (TiO₂), crucial in harsh environments like marine or chemical processing.
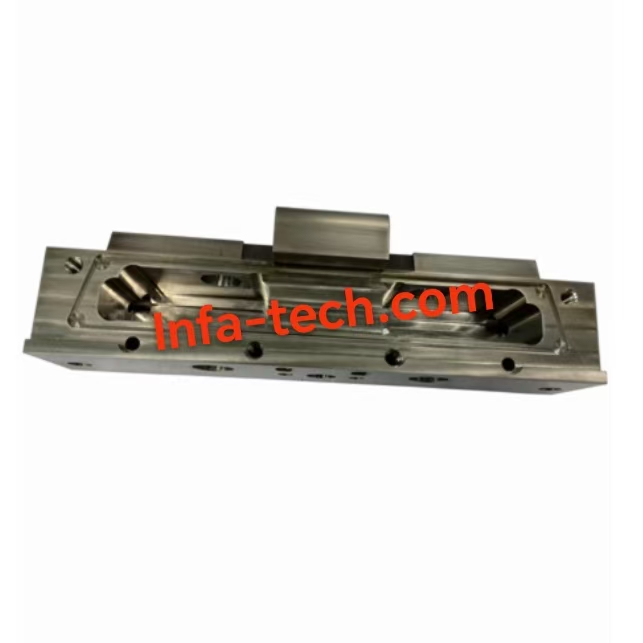
Second. Improved Fatigue Resistance:
Surface irregularities act as stress concentrators, initiating cracks under cyclic loads. Polishing removes these imperfections, extending the component's fatigue life, vital in aerospace and automotive industries.
Third. Reduced Friction and Wear:
A polished surface minimizes friction in moving parts, such as engine components or medical devices, reducing wear and enhancing longevity.
Fourth. Biocompatibility and Hygiene:
In medical implants (e.g., joint replacements), a smooth surface prevents bacterial adhesion, reduces tissue irritation, and ensures easier sterilization, critical for patient safety.
Fifth. Aesthetic Appeal:
Polishing provides a sleek, reflective finish desirable in consumer products (e.g., jewelry, watches) and architectural elements, enhancing visual and market value
Sixth. Precision in Assembly:
Smooth surfaces ensure tighter tolerances and better sealing in high-precision applications, such as aerospace fittings or semiconductor equipment, preventing leaks or misalignments.
Seventh. Prevention of Material Adhesion:
In chemical or food processing, polished surfaces resist deposit buildup, simplifying maintenance and reducing contamination risks.
Industry Examples:
- Aerospace: Polished components withstand fatigue and corrosion in critical structures.
- Medical: Implants benefit from biocompatibility and hygiene.
- Automotive: Reduced friction improves engine efficiency.
- Consumer Goods: Aesthetic polish boosts product appeal.
In summary, polishing titanium optimizes its inherent properties, ensuring reliability, durability, and functionality across diverse applications.